Kinesys helps shape Ed Sheeran tour
- Details
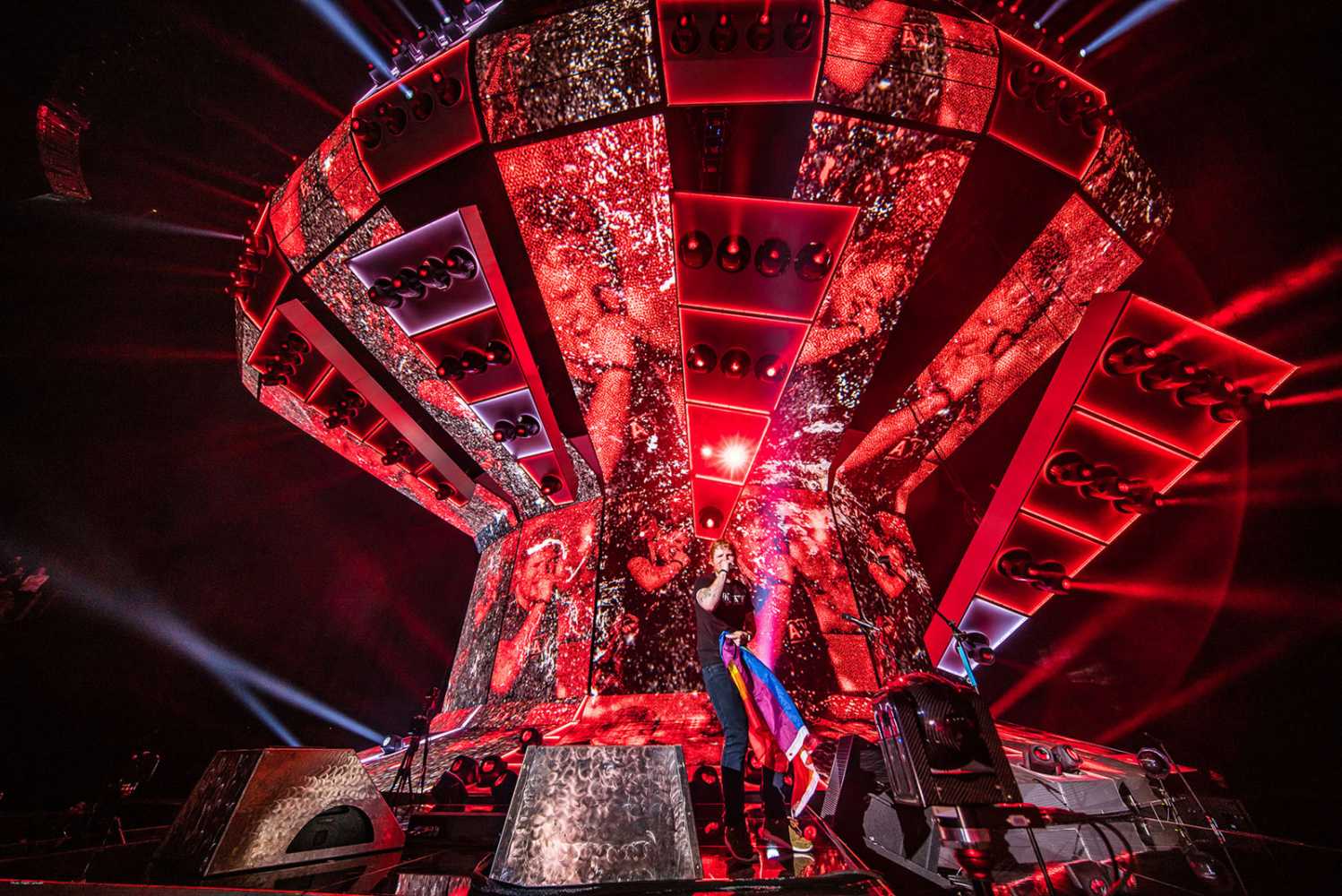
The impressive lighting and scenography design which is helping Sheeran wow the crowds and impress the critics has been created by Mark Cunniffe.
The Kinesys system and control was recommended by Mike Oates, director of UK based Lights Control Rigging (LCR), the tour’s lighting equipment and crew supplier in combination with SES in the US.
The Kinesys equipment includes four Kinesys DigiHoist Plus (63 Amp) and eight DigiHoist (32 Amp) intelligent chain hoist controllers, 42 x Kinesys LibraCELL load monitoring cells and 12 x Liftket variable speed 500kg hoists fitted with Kinesys Elevation 1+ drives. The system was configured and built during the prep in LCR’s warehouse before being dispatched to the tour.
It has been purchased by audio, rigging, motors and automation supplier, Salisbury based Major Tom Ltd., and is being co-ordinated on the road by Steve Bliss and operated by Omar Franchi from the rigging crew.
All the tour’s production elements are being overseen by production manager Chris Marsh.
Steve’s first job of the day is assisting the other lighting crew in building the mother-grid, which weighs a hefty 11 tonnes before being loaded with any kit!
This is lifted using 30 x 2-tonne single-reeved chain motors each fitted with a 4.75T Kinesys LibraCELL for full monitoring and controlled via the Kinesys DigiHoist Plus intelligent hoist controllers.
The mother grid is pre-rigged with 47 of a total of 52 x 1 tonne chain motors (five are hung daily) which are each fitted with encoders for full positional control, and these are controlled by the 8 x 32A Kinesys DigiHoists.
These sub-hung hoists control lifting the lighting and video elements into place during the build.
That comprises five curved video screens (crowns); four lighting crowns which sit in between each video screen and five video screens dubbed ‘the ceiling’ which sit horizontally above the stage that have triangular lighting “pods” filling the gaps. Additionally, there are five video screens making up a back wall and giving a continuous ‘flow’ of video surface from the top header, through the ‘ceiling’ and down the back finishing at stage level where the video angles back on to the stage.
The four lighting pods are flown on the 12 x 500kg vari-speed Kinesys Liftket motors which move into a series of configurations during the show.
These Liftkets are rated with a 10:1 safety factor and are also fitted with LibraCELLs as they fly above the artist’s head during the show.
The margins for movement are very tight and a key reason that Kinesys was chosen was for its accuracy, reliability and stability.
Joining the 12 x DigiHoist controllers in the custom motor control ’dolly’ onstage is a Kinesys Mentor E-Stop hub giving SIL3 e-stop protection over the entire system. There is also an Ethernet switch for the Kinesys network and a LibraPRO control unit to manage the Libra cells. The dolly is powered via a set of 300A Powerlock connectors.
By the time the grid is fully loaded with all the kit and cables for the show, it weighs 32 tonnes. When it is taken out to show height, all the sub-hung motors are simultaneously run out - involving 1.6 Km of chain - pulling an average of 260A per phase!
Sitting next to the dolly is a Kinesys PDES (power distribution and emergency stop) control rack containing two PDES units (active and backup) and one array dealing just with data to the Elevation 1+s.
Controlling all the movement is the custom Vector computer rack, containing two PCs - for full redundancy- running Kinesys’ Vector, with a KVM for easy switching between the two. Three active screens are utilised, one for Vector, one for the LibraCELL feedback and one receiving a feed from the FOH camera … so they can see the movement at all times during the show. A UPS is in place for back-up power if needed.
During the day, this rack is positioned upstage centre where Steve and Omar have a clear view of everything being built, and once everything is in the roof, settled and trimmed, it is moved to its show operation position stage right. Three E-Stops are located around the stage for safety.
The Vector system works from two showfiles – one for the build / de-rig and one for the show.
“The Kinesys products are fantastic” states Steve Bliss. “They do exactly what is needed, and are very accurate and safe. With the DigiHoist controllers reading the encoders, fault-finding is quick and easily”.
Dave Weatherhead comments: “It’s a fantastic reference for all our products to be on a tour of this profile, prominence and length, a big investment for Major Tom and a great endorsement from a production specialist like Mike Oates as to the advantages that Kinesys can bring to a complex show like this”. He also noted that, “Having spent some time with the production and crew I can wholeheartedly say that everyone I have met on the show is, without exception, totally professional. They also happen to be some of the nicest individuals I have met in the touring world.”
(Jim Evans)